Reference
With aim

As a total solution provider specializing in IT technology and factory automation with more than 30 years of experience, we provide know-how to build various projects for companies of all sizes across smart factory industries in Korea and abroad.
Implementation Examples
SFA - Factory Automation System Implementation Smart Factory
SFA
Project :
Factory Automation System Implementation
Period :
2011–2012
Industry :
Semiconductor Back-End PKG
Provided Solution
MES, MDM, RPT, QMS, WMS, EAP
Key Achievements
Established an improved MES (Glomis 3.0) in China and domestically (Cheonan) to digitize various activities managed in factories. This provided foundational data for cost and production management, enhanced product quality through equipment automation, and built an integrated and standardized Global Standard MES system that maximized factory efficiency.
MES and Master Data Management system construction
Production reporting, quality management & warehouse management systems
Semiconductor PKG frontend equipment automation (MC3I) implementation
Features and Benefits
– Enhanced and standardized quality control
– Unified master data for all company sites
– Upgraded outdated IT infrastructure
– Equipment online automation
– Real-time production information management
– Data-driven factory control automation
– Real-time material status (input/end) monitoring
– Enhanced KPI management (equipment, production performance, materials)
– Real-time inventory tracking and accurate material usage confirmation
– Standardization of manufacturing operations
– Aiming to eliminate human error and quality incidents
– Automated tracking and remote equipment control
– DA: Remote management of wafer maps and viewer
– WB: Wire coordinate analysis and interlock system
BOE - OLED CIM ProjectSmart Factory
BOE
Project :
OLED CIM Project
Period :
2016/05 ~ 2022/07
Industry :
Display
Provided Solution
MES, EAS, MCS, FDC…
Key Achievements
–
Features and Benefits
In the OLED business, securing high quality is a decisive factor that directly impacts business performance. The core foundation of this quality enhancement lies in factory standardization. In Company B’s OLED factory standardization project, aim Systems’s standardized systems and processes were applied across manufacturing, process, system, and quality departments. This established a unified consensus and communication framework, significantly strengthening the company’s manufacturing foundation and its quality competitiveness. Based on its accumulated expertise from various standardization projects, aim Systems combines its clients’ existing standards with best practices from other companies to create superior benchmarks. It then improves operational processes to enable faster decision-making and structured quality assurance.
When all services are provided by a single vendor, system integration timelines are shortened, and collaboration during the implementation phase becomes much more stable. Through multiple projects with aim Systems during the OLED plant construction, Company B naturally carried the accumulated experience and expertise into subsequent projects. This led to the formation of a close communication system among project stakeholders, fostering a collaborative culture that transcends organizational boundaries in pursuit of shared success. Such accumulation of experience strengthens continuity between past and future projects and maximizes the effectiveness and satisfaction of the One-Stop solution approach.
Improving equipment efficiency and productivity—common goals across all manufacturers—requires not only the automation of individual equipment but also a deep understanding of on-site operations and close cooperation with equipment manufacturers. Since a factory standardization project covers all upstream and downstream equipment, collaboration with a variety of process and automation equipment vendors is essential for each project. Repeated efforts toward productivity improvement and the accumulation of measurable results contribute not only to technical achievements but also to the professional growth of every team member involved. As a result, the collaboration between teams with a shared “DNA of success” enhances the completeness and overall quality of the project.
csot - LCD/OLED CIM ProjectSmart Factory
CSOT
Project :
LCD/OLED CIM Project
Period :
2015/04 ~ 2023/12
Industry :
Display
Provided Solution
MES, EAS, MCS
Key Achievements
–
Features and Benefits
Company C entered China’s display market in its formative years and emerged as a pioneering enterprise that helped define industry-wide benchmarks. aim Systems played a pivotal role in this journey by leading the comprehensive standardization of Company C’s first factory—widely regarded as the birthplace of China’s display industry. This project extended far beyond merely establishing standard procedures; it built an operational framework that enabled the entire organization to communicate in a unified language and make swift, coordinated decisions. This foundation enabled Company C to achieve rapid and sustainable growth in the competitive display market.
While establishing its OLED display production line, Company C became the first in China to successfully adopt a Linux-based Enterprise Automation System (EAS). Centered around its Manufacturing Execution System (MES) and Material Control System (MCS), the EAS features a lightweight operating platform, flexible scalability, and efficient maintenance enabled by open-source technologies. aim Systems, as the core implementation partner, was responsible for designing operational scenarios, standardizing system interfaces, and constructing real-time integration frameworks. The resulting system has become a widely referenced benchmark in the industry for both operational efficiency and system reliability.
Company C has strategically focused on automation systems centered around MES and MCS to strengthen its capabilities in real-time process control and production execution. This approach not only boosted short-term productivity but also laid the groundwork for data-driven process analysis and quality prediction systems. As a result, Company C has significantly enhanced its responsiveness and accuracy in customer service. Leveraging these system-driven competitive advantages, the company now ranks second in China’s display market. aim Systems continues to serve as a trusted long-term partner, having helped architect and drive this sustained growth.
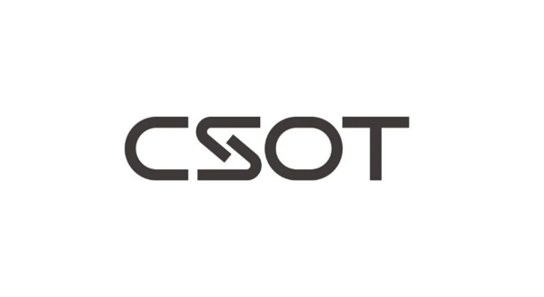
Tianma - LCD/OLED CIM ProjectSmart Factory
Tianma
Project :
LCD/OLED CIM Project
Period :
2021/04~
Industry :
Display
Provided Solution
MES, EAS, MCS, RPT…
Key Achievements
–
Features and Benefits
Company T, known for its proprietary manufacturing technologies and differentiated process strategies in the LCD and OLED sectors, demands exceptional technical precision and meticulous project execution. aim Systems has successfully delivered multiple LCD and OLED production line projects tailored to T’s advanced technological requirements. Notably, aim Systems led the largest and most critical OLED project within T’s business, fulfilling stringent demands through the seamless integration of diverse processes and equipment. This collaboration—combining T’s technological leadership with aim Systems’ integration capabilities—has become a benchmark in the advancement of next-generation display manufacturing systems.
T and aim Systems have cultivated an ongoing technical partnership that goes beyond one-off contracts. Currently, the two companies are working together on new module factories and OLED plant projects. Each initiative presents unique requirements—ranging from new equipment specifications and module interface methods to customized control logic—but aim Systems’ deep understanding of T’s processes and system architecture allows for rapid adaptation and high-quality execution. This accumulated experience enables simultaneous achievement of speed and quality in the design, development, and implementation of new production lines, enhancing project completeness and customer satisfaction.
To remain competitive in the next-generation display market, T is pursuing both precision in process technology and flexibility in production operations. aim Systems is seen as a critical technology partner in realizing this vision. With a thorough grasp of T’s manufacturing strategies and extensive hands-on experience, aim Systems is at the forefront of equipment integration, system design, and the development of standardized models aligned with T’s strategic goals. Looking ahead, aim Systems is well-positioned to play a central role in advancing key initiatives such as OLED process innovation and smart module line implementation—further strengthening T’s global manufacturing competitiveness.
Visionox - OLED CIM ProjectSmart Factory
Visionox
Project :
OLED CIM Project
Period :
2017/05 ~ 2021/12
Industry :
Display
Provided Solution
MES, EAS, MCS, RPT …
Key Achievements
–
Features and Benefits
Company V is a specialized manufacturer dedicated to OLED displays, recognized for building production environments that demand exceptional precision and advanced technical expertise. From its very first facility to the upcoming fifth plant, aim Systems has participated in the construction of every OLED production line, building a long-standing and deep-rooted technical partnership with the company. Given the characteristics of OLED manufacturing—where fine-tuned equipment calibration, strict process control, and real-time quality management are essential—aim Systems has played a critical role in stabilizing and advancing V’s manufacturing foundation by integrating a wide range of high-spec equipment into a unified, reliable system.
More than just a solution provider, aim Systems has earned V’s trust through its deep understanding of OLED-specific processes and its customized, responsive approach to each project. As a result, Company V has consistently recognized aim Systems as an outstanding partner across multiple projects, presenting the company with several awards for excellence in collaboration. This trust has fostered an exceptionally close technical and cultural partnership between the two companies. Even when plant requirements differ, aim Systems has repeatedly delivered systems optimized for V’s operational needs, significantly contributing to both manufacturing stability and internal technological advancement.
Looking ahead, Company V is preparing to launch its fifth production facility, expected to become a core hub for OLED manufacturing. Once again, aim Systems is being positioned as a key technology partner. This project requires not only heightened process complexity but also uncompromising operational stability. Drawing from its extensive experience supporting factories 1 through 4, aim Systems is fully equipped to meet these challenges with its expertise in OLED equipment standardization, integrated operations, and customization. As V’s strategic ally, aim Systems is committed to co-developing and implementing advanced solutions tailored to OLED production, playing a central role in strengthening the company’s long-term competitiveness.
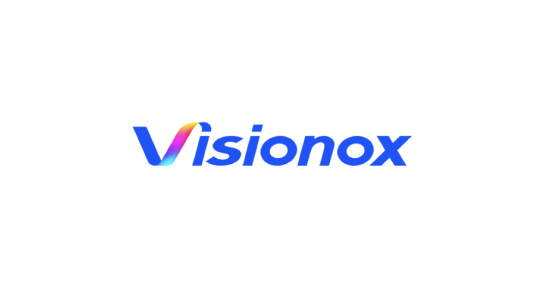
Truly - LCD/OLED CIM ProjectSmart Factory
Truly
Project :
LCD/OLED CIM Project
Period :
2015/01 ~ 2021/09
Industry :
Display
Provided Solution
MES, EAS, MCS
Key Achievements
Features and Benefits
Company T has built cost-effective production lines by introducing second-hand display manufacturing equipment from major Korean manufacturers such as S and L. However, integrating equipment from different makers, generations, and control systems into a unified production line requires advanced control engineering and deep system integration expertise. Leveraging years of experience in equipment retrofitting and standardization, aim Systems provided a one-stop solution to standardize control layers and system architectures across all of T’s factories. In particular, aim Systems demonstrated core capabilities in interpreting outdated I/O signals, converting protocols, and enabling real-time integration of legacy equipment.
Amid the complexities of heterogeneous equipment environments, aim Systems provided an end-to-end solution covering the full lifecycle—from planning and design to retrofitting, integration, and operation standardization—through a single point of contact. This helped reduce project timelines by eliminating communication overhead across multiple vendors and enabled seamless internal collaboration within Company T. The success of several projects led by aim Systems has since been expanded company-wide, ensuring continuous equipment operations without disruption. As a result, T successfully built a unified control and data integration system that overcame the limitations of individual equipment and stabilized mass production.
Company T’s manufacturing strategy focuses on flexibly utilizing second-hand equipment to reduce fixed costs while achieving high-performance production. Given the high barriers to entry, a reliable technical partner is essential. Throughout the project, aim Systems delivered additional value through equipment-specific optimization, standardized technical responses, and the cultivation of a collaborative work culture, thereby helping T secure core manufacturing competitiveness. This strategy—enabled through close cooperation with aim Systems—has become a best practice that simultaneously achieves financial efficiency and technological excellence.
– Early Achievement of Productivity Recovery and Quality Stabilization through Reuse of Existing Equipment and Site-Optimized Automation Strategy By reusing existing equipment and implementing an automation strategy tailored to on-site conditions, the project achieved rapid recovery of productivity and early stabilization of quality. This effectively reduced the customer’s risk during production transition and provided tangible proof of investment value.
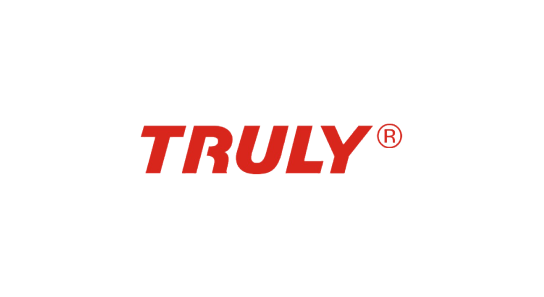
BOE - LCD CIM ProjectSmart Factory
BOE
Project :
LCD CIM Project
Period :
2014/04 ~ 2020/12
Industry :
Display
Provided Solution
MES, EAS, MCS, RPT…
Key Achievements
–
Features and Benefits
Company B played a landmark role in establishing industry standards during the development of China’s display industry. aim Systems joined early in Company B’s LCD business journey, co-leading projects focused on standardizing equipment operations, quality control, and system frameworks. This initiative became a pioneering case in establishing consistent standards and collaborative systems across production, equipment, process, quality, and IT domains. It has since been widely shared as a benchmark among other manufacturers in China. The success of Company B’s standardization efforts significantly improved not just quality consistency but also decision-making speed and accuracy, responsiveness to quality variances, and communication efficiency with partners. These outcomes became a critical foundation for Company B to secure trust and strategic partnerships with global customers.
Company B marked a major milestone in the evolution of global display technology by becoming the first in the world to mass-produce 10.5-generation LCD displays. Given the complexity of handling ultra-large glass substrates, process stability was a key challenge. aim Systems played an essential role in early equipment setup, ensuring quality data alignment, and managing risks during initial production. The standardized operation system supported by aim Systems enabled consistent quality and efficient production in large-panel processes. As a result, Company B secured long-term orders from major global TV manufacturers—further widening its lead over competitors in both technical excellence and commercial performance.
The collaboration with Company B also opened new doors for aim Systems. With Company B’s standardization and quality achievements widely recognized across the industry, many display manufacturers began seeking aim Systems’ partnership. This led to aim Systems conducting continuous projects across China’s display sector, contributing to structural improvements and greater production competitiveness industry-wide. Ultimately, Company B achieved the number one position in the global LCD market. This achievement not only reflects Company B’s technological edge but also serves as a powerful testament to the value of operational standardization and robust quality systems. aim Systems has firmly established its position as a strategic implementation partner at the heart of this success.
BMOT - Micro OLED CIM ProjectSmart Factory
BMOT
Project :
Micro OLED CIM Project
Period :
2018/10 ~ 2020/01
Industry :
Display
Provided Solution
MES, EAS
Key Achievements
–
Features and Benefits
Company B spearheaded a new era in next-generation display technology by establishing one of the industry’s first production lines dedicated to Micro OLED. This joint project between Company B and aim Systems went far beyond conventional manufacturing—it was a landmark initiative that defined new industry standards. aim Systems led the project from the ground up, overseeing everything from initial planning and process design to quality benchmark development and system architecture, despite a complete lack of existing frameworks. Thanks to this initiative, Company B secured the technical stability and operational foundation required to successfully enter the Micro OLED market.
The Micro OLED sector demands a hybrid manufacturing environment—merging the ultra-fine precision of semiconductor processes with the large-area, multi-step nature of display production. One of the biggest challenges was the immaturity of participating equipment vendors, which required constant troubleshooting and frequent adjustments to specifications. Inter-process coordination issues and unstable quality added to the complexity. In the midst of these challenges, aim Systems played a critical role in stabilizing the operation by systematically establishing process standardization, equipment interconnection logic, and quality monitoring systems. As a result, the project became a model case in the Micro OLED field and has since been adopted as the de facto industry standard by numerous other companies.
Even after the project’s successful completion, Company B has continued to seek aim Systems’ technical expertise and execution capabilities. aim Systems has offered long-term support to ensure the stability of Company B’s Micro OLED business—improving operational standards, validating new equipment integration, and redesigning quality criteria in response to evolving product architectures and process conditions. This partnership has matured beyond conventional consulting into an on-the-ground, field-focused technical alliance. aim Systems remains a practical and strategic partner, playing a vital role in helping Company B solidify its leadership position in the Micro OLED market.
HKC - LCD CIM Project Smart Factory
HKC
Project :
LCD CIM Project / MOD CIM Project
Period :
2019/08 ~ 2020/12 , 2020/06 ~ 2021/10
Industry :
Display
Provided Solution
MES, EAS, MCS
Key Achievements
–
Features and Benefits
Company H entered the display business relatively late and operated with a limited investment scale compared to larger enterprises. Nevertheless, it became a leading example of quickly delivering results in the market through excellent project execution efficiency and internalization of organizational capabilities. Through its collaboration with Company H, aim Systems presented an execution strategy that maximized outcomes within limited resources. In particular, aim Systems intensively supported advanced training for client personnel and closely guided on-the-ground standardization activities. As a result, Company H built a self-reliant system that enabled its internal staff to operate and continuously improve the system without external dependence, even after project completion. This led directly to long-term maintenance cost savings and enhanced operational stability.
While focusing on an LCD-centered display business, Company H did not stop at the initial panel processes. It expanded into downstream module factory operations, achieving vertical integration. During this process, aim Systems delivered solutions for production standardization, quality control, and MES system integration, ensuring continuity and operational optimization across all processes. Especially in high-intensity short-term projects such as capacity expansions or line modifications, aim Systems designed execution processes that ensured both stable quality and operational consistency—enabling Company H to respond flexibly to change and rapidly improve productivity. As a result, Company H established itself as a competitive LCD module manufacturer in China.
Building on the success of the initial project, Company H continues to respond swiftly to market demand through ongoing expansion and modification of existing production facilities, consistently maintaining a high market share. This reflects Company H’s philosophy of not remaining focused on short-term achievements but simultaneously pursuing long-term operational improvements and strategic investment. In line with this direction, aim Systems has continued to provide follow-up support at each stage of Company H’s business growth—including equipment changes, process expansion, and quality standard redesign. This has played a key role in helping Company H maintain a structure capable of stably managing complex manufacturing environments using its internal capabilities. This collaboration model represents a quintessential example of aim Systems’s customer independence philosophy and long-term partnership strategy.
Tianma - MOD CIM ProjectSmart Factory
Tianma
Project :
LCD/OLED CIM Project
Period :
2023/05 ~ 2025/12
Industry :
Display
Provided Solution
MES, EAS, MCS, RPT…
Key Achievements
–
Features and Benefits
Company T has established a stable production base in the OLED module sector, particularly for the IT and automotive display markets. Recently, it has accelerated its transition to a next-generation manufacturing and operations environment through an ongoing project with aim Systems. This initiative targets OLED module lines, which inherently have high process complexity, aiming for standardization, quality system enhancement, and improved real-time operational visibility. The collaboration is progressing smoothly and stably. aim Systems is contributing to minimizing initial implementation risks and maximizing operational efficiency by providing tailored execution strategies and system designs that reflect Company T’s on-site characteristics and production flow.
One of the most notable achievements of this project is Company T’s successful implementation of a virtualized manufacturing operations environment—an approach rarely attempted within the industry. This was a strategic move to depart from traditional physical infrastructure, aiming to boost flexibility, scalability, and maintenance efficiency. aim Systems played a pivotal role in facilitating this transition. Additionally, aim Systems successfully supported the migration of key systems whose service had been discontinued in existing factories, ensuring their stable operation in the new environment without any production downtime. This stands as a best-practice case of seamless technological transition.
Although Company T began with a relatively limited initial investment, it has achieved clear project outcomes through strong strategic direction and execution. It now looks forward to pursuing follow-up initiatives together with aim Systems. The new virtualization-based infrastructure also opens the door to various expansion possibilities, such as additional process automation and advanced smart factory capabilities. aim Systems, in turn, highly values Company T’s technological strength and execution capabilities demonstrated through this project and believes a solid foundation for a long-term collaborative model has been established. Going forward, aim Systems will continue to serve as an execution-focused technology partner, co-designing and supporting Company T’s ongoing transformation and growth.
Customer & Partner
We lead the way in Smart Factory Digitalization through a technology collaboration model with our customers and partners.
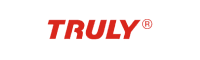
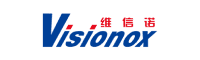